Engineering Plastics
Polycarbonate (PC)
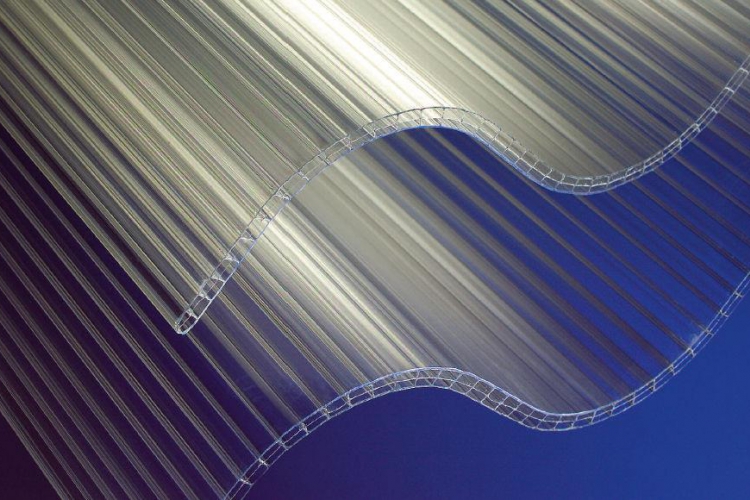
Transparency, excellent toughness, thermal stability and a very good dimensional stability make Polycarbonate (PC) one of the most widely used engineering thermoplastics. Compact discs, riot shields, vandal proof glazing, baby feeding bottles, electrical components, safety helmets and headlamp lenses are all typical applications for PC.
Polycarbonate is most commonly formed with the reaction of bis-phenol A (produced through the condensation of phenol with acetone under acidic conditions) with carbonyl chloride in an interfacial process. PC falls into the polyester family of plastics.
Polycarbonate remains one of the fastest growing engineering plastics as new applications are defined; global demand for PC exceeds 1.5 million tons.
Properties
Polycarbonates are strong, stiff, hard, tough, transparent engineering thermoplastics that can maintain rigidity up to 140°C and toughness down to -20°C or special grades even lower. The material is amorphous (thereby displaying excellent mechanical properties and high dimensional stability), is thermally resistant up to 135°C and rated as slow burning. Special flame retardant grades exist which pass several severe flammability tests.
Constraints to the use of PC include limited chemical and scratch resistance and it's tendency to yellow upon long term exposure to UV light. However these constraints can be readily overcome by adding the right additives to the compound or processing through a co-extrusion process.
Applications
In recent years Polycarbonate blends have become increasingly commercially important. PC is widely used in blends due to its excellent compatibility with a range of polymers. Typical blends include rubber modified PC, improving impact properties, PC/PBT blends, which allow toughness to be retained at lower temperatures and having improved fuel and weather resistance. Amongst the most significant are those incorporating ABS (Acrylonitrile Butadiene Styrene). PC/ABS blends exhibit high melt flow, very high toughness at low temperatures and improved stresscrack resistance compared to PC.
All Blends are produced using a compounding step to blend the polymers. This compounding technology is very important for creating the optimal morphology and interaction between the two phases. In combination with the right additive know-how (flame retardant, stabilization, reinforcement) blends are obtained with an optimally balanced set of properties.
PC finds usage in a host of markets, notably in the automotive, glazing, electronic, business machine, optical media, medical, lighting and appliance markets.
Typical examples of applications of technology are within:
- power distribution (covers and housings)
- connectors
- electrical household appliances
- mobile phones
- electrical chargers
- lighting
- battery boxes
- automotive lighting
- head lamp lenses
- dashboards
- interior cladding
- exterior parts (bumpers, bodypanels)
- power tools
- baby bottles
- water dispensers
- garden equipment
- furniture (office & institutional)
- sporting goods
- medical applications