Engineering Plastics
Polyamide (PA)
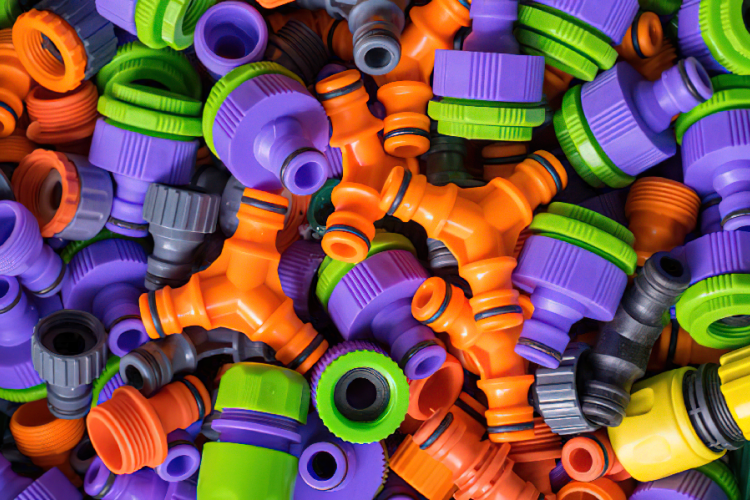
The name "nylons" refers to the group of plastics known as polyamides. Nylons are typified by amide groups (CONH) and encompass a range of material types (e.g. Nylon 6,6; Nylon 6,12; Nylon 4,6; Nylon 6; Nylon 12 etc.), providing an extremely broad range of available properties. Nylon is used in the production of film and fibre, but is also available as a moulding compound.
Nylon is formed by two methods. Dual numbers arise from the first, a condensation reaction between diamines and dibasic acids produces a nylon salt. The first number of the nylon type refers to the number of carbon atoms in the diamine, the second number is the quantity in the acid (e.g. nylon 6,12 or nylon 6,6).
The second process involves opening up a monomer containing both amine and acid groups known as a lactam ring. The nylon identity is based on the number of atoms in the lactam monomer (e.g. nylon 6 or nylon 12 etc).
Properties
The majority of nylons tend to be semi-crystalline and are generally very tough materials with good thermal and chemical resistance. The different types give a wide range of properties with specific gravity, melting point and moisture content tending to reduce as the nylon number increases.
- High strength and stiffness at high temperature
- Good impact strength, even at low temperature
- Very good flow for easy processing
- Good abrasion and wear resistance
- Excellent fuel and oil resistance
- Good fatigue resistance
- PA 6 has excellent surface appearance and better processability than PA66 (due to its very low viscosity)
- Good electrical insulating properties
- High water absorption and water equilibrium content limits the usage
- Low dimensional stability
- Attacked by strong mineral acids and absorbs polar solvents
- Proper drying before processing is needed
Applications
Nylon fibres are used in textiles, fishing line and carpets. Nylon films is used for food packaging, offering toughness and low gas permeability, and coupled with its temperature resistance, for boil-in-the-bag food packaging.
Moulding and extrusion compounds find many applications as replacements for metal parts, for instance in car engine components. Intake manifolds in nylon are tough, corrosion resistant, lighter and cheaper than aluminum (once tooling costs are covered) and offer better air flow due to a smooth internal bore instead of a rough cast one. Its self-lubricating properties make it useful for gears and bearings. Electrical insulation, corrosion resistance and toughness make nylon a good choice for high load parts in electrical applications as insulators, switch housings and the ubiquitous cable ties. Another major application is for power tool housings.