Additives
Lubricants(LUB)
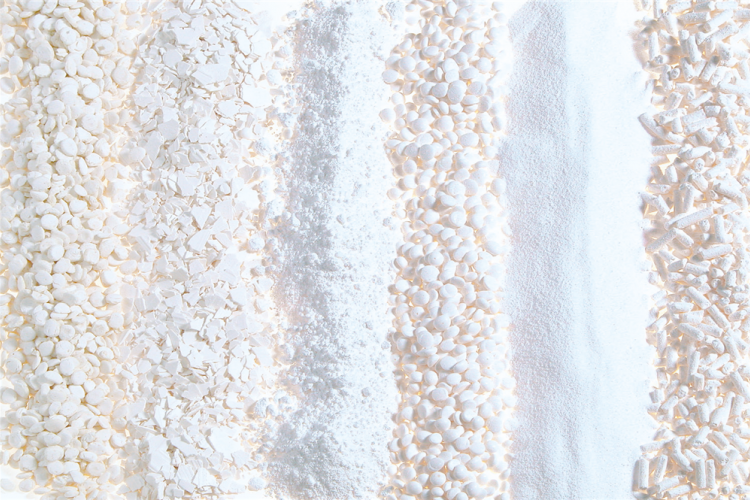
Lubricants are additives that improve the processability of the resin and prevent damage to the molding equipment by reducing friction (external lubricants), and by lowering the bulk viscosity (internal lubricants). Typical external lubricants are metallic soaps, fatty acids, paraffin and low MW polyethylene. These compounds migrate to the interface between the molten resin and the metal surface of the processing equipment and reduce friction. Internal lubricants promote the flow of the resin and facilitate mold filling. Common internal lubricants are fatty esters, EVA waxes and oxidized polyethylene. A third class of processing additives is mold release agents (de-molding agents), which keep the plastic product from sticking to the mold and reduce surface imperfections. Silicone oils, graphite, zinc stearate, and molybdenum disulfide are often used for this purpose if the aforementioned lubricants do not provide sufficient mold release.
Lubricants affect processing and quality of the final material. Numerous relationships of the lubricant are crucial for selection.
The key criteria for selecting lubricants are:
- Compatibility with the host resin
- No adverse effect on properties
- Easy introduction
- Approval for specific applications (such as food or pharmaceuticals)
- No (or almost no) retarding effect on gelation
- No reduction in melt strength and extensibility
- Good transparency
- Improved plate-out performance